Stud Walls
Often you can’t access the wall without removing weatherboard or plaster. However, the stud bays in my house are open – no noggings, few wires. Therefore I’ll try to pump in insulation via (1) top (2) bottom or (3) a hole in the plaster. The weatherboards form a water barrier (seal the gaps) but stills, there’s a risk of moisture. Best use a moisture-resistant insulation.
Weatherboard Wall External with Foam (external frame exposed)
Where the frame is exposed there are more options. Old Queenslanders have 70mm studs, which can be exposed during reno if removing the weatherboards.
We want an minimum R2.8, but R3.5 is better on exposed western walls. This can be made up of:
- 70mm batts: R1.6
- Wall normal airspace: R0.2 (R.0.6 if reflective)
- 40mm XPS : R1.0
- This gives a total of R2.8 which is just enough. A detail is below. Paint it white to reflect the sun and shade it.
Using a breathable wrap and XPS polystrene , this construction is:
- vapour permeable
- rainscreen to allow drying of boards
- XPS stops thermal bridges. XPS costs $14/m² for 40mm
Other alternatives would be:
- Optional: Add reflective layer : I don’t like these much: can be ineffective due to dirt and/or need a gap. But by adding over the battens to this construction it would add R0.4 for little effort and cost ($3/m2). Consider for walls in high sun. Use a ‘breather’ foil (i.e. with micro holes)
- Aircell: About $10/m2 and provide R0.2 (Aircell) plus 0.6 reflective, so similar to XPS 40mm. It would be easier to install and avoids the need for a building wrap. The airtightness and permeance are questionable. Same reflective problems.
- Add another 75mm wall of studs and increase batt insulation. Easier but no rainscreen.
External Frame Unexposed, Internal Frame Exposed
The back of the weatherboards are exposed. Some water ingress is likely from hard wind-driven rain.
Ideally we’d add a drainage/airtight plane behind the weatherboard, using a building fabric. However, this is often impractical because you need a ‘open to daylight’ exit for any collected water. The any nogs/sills/walls below make this hard.
Next best (IMHO!) is to at least have a gap between the weather boards and insulation. This stops wicking and allows better drying. Combine this with moisture resistant insulation for (hopefully) an okay system.
Option 1: EPS Unbacked Foam
- EPS 50mm cut and fitted between studs.
- EPS is $15/m². Labour intensive. Foam around edges if you’re keen. XPS is water resistant so this is durable.
- 50mm EPS is R1.3, add gap air and films for R1.6 .
Option 2: EPS Foil Backed Foam
- As for #1 but foil backed foam
- Adds a nice +R0.5 in the (now reflective) air gap
- Reduces breath ability. In this situation that’s probably ok.
- 50mm EPS “Foilboard” is $29/m²
Option 3: Semi-rigid Batt
- A semi-rigid batt could maybe maintain a gap. Use polyester or rockwool for moisture resistance.
- It would be easy to fit but not an airseal, and more likely to absorb moisture.
External Frame Unexposed, Internal Frame Unexposed
It’s expensive and difficult but possible. The outer wall must be ‘reasonably’ watertight. Good weatherboards might be okay, but unknown. Experiments required.
Option 1: Blow in with machine
- Knauf Supafil CarbonPlus is reportedly hydrophobic. Material cost is about $10/m² but only available installed.
Option 2: Stuff in
- Unknown if feasible
Sub Floor Insulation
The subfloor can be insulated, but it’s a bit harder than walls or roof, since the insulation wants to fall out. There is a lower temperature difference compared to walls or roof (think 10°C instead of 40°C for a roof) so reflective insulation is less effective (note the ‘R Value’ is a useful simplification but hides this – details).
So foil or ‘aircell’ type products might be less effective compared to bulk insulation. Some manufacturer suggest rolling over the joists, and others cut between. A roll-over and screw-fix of particle floor would likely be okay and a fast way to be some insulation.
Bulk batts are difficult to install well and tend to get torn.
XPS polystrene foam works well. It’s about $10/m² for 40mm thick. You can get it in any size. A convenient size is 440 or 590 for 450/600 joists. It can then be push fitted and a foam gun is used to seal. Easy for timber but for C channel steel, this leaves a 10mm gap. Before the subfloor is sealed/weatherproof, be careful to not trap water – a small hole is cut and then sealed with foam on completion.
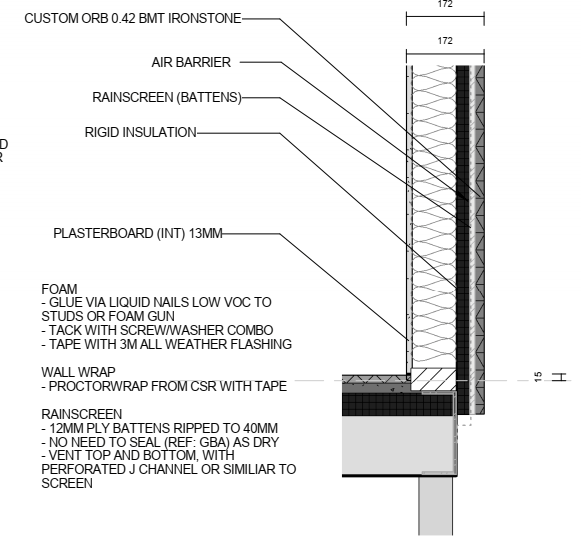
5 thoughts on “Insulating a Queenslander”
Hi, I have a freezing cold house and I love in S.e qld. I need help insulating it. Any recommendations. It’s a raised double story, with single brick and shaded much of the morning by a hill
Hi rokaya, is the ceiling already insulated? have you considered doing something with the floor? Do you find the floor itself (timber?) freezing. I am planning to put down a floating floor over mine. There is a thin layer rolled out over the existing floor before you lay the floating floor which would provide a level of insulation. My home is 1950s, so am also considering double-glazing our timber casement windows by installing another glass pane from other windows no longer being used. Still, it’s tricky to fully seal the frame around the windows when they’re closed.
One thing that really helped was when I replaced our ceiling fan in the bathroom, it has a set of flaps at the top above the fan. The flaps close by gravity when the fan is not operating and are pushed open by the power of the fan blowing. It really stopped the cold air from the ceiling re-entering the inside of the house.
There are passive means to redirect air and capture and store heat as well – try doing some googling. Whether any of those methods are practical in an urban setting for an existing house is another question.
Any recommendations about noise insulation.
House is depending of the season cold or hot, but it’s the noise that is a problem for me.
Windows are let the most noise in.
Double glazing or replacing thin panes with 10mm thick ones is an option.
Sealing any gaps around the windows/doors as well.
For walls: thicker batts if installing uninsulated walls.
Thicker wall lining panels: gyprock (can be doubled) or thick plywood.
There are some new sound deadening materials (rubber sheets) available these days, often used for car interiors, that are very effective.
Mass loaded vinyl is another material for noise absorption.
if the internal frame is exposed; I would seal obvious gaps in weatherboard. Then install a semipermeable vapour barrier to give separation between the weatherboards and insulation this should stop wicking of any small amount of water that makes it through. The studs are in the way of the vapour barrier so I’d install the barrier with a staple gun wrapping the studs. Its not perfect but queenslanders are old homes and this should keep moisture off the insulation and going to were it has gone for 80+ years. if the aim is to air-condition, the insulation will mean far less moisture builds up in the wall cavity than without it. 70mm wool insulation can be used no air gap is possible, but the perfect is the enemy of the possible.